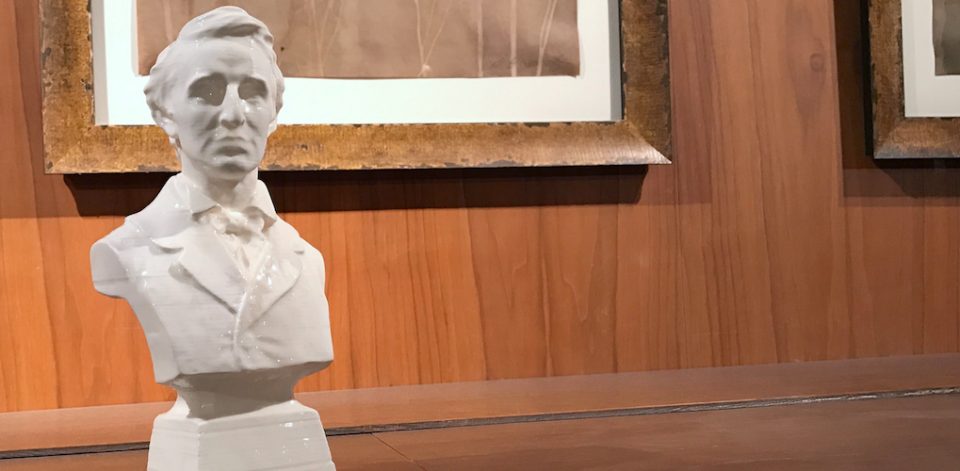
By Humtech RITCs on November 7, 2016
Last time we looked at how photogrammetry was used to reconstruct the 1898 bust sculpture of Henry David Thoreau. Now we will see how 3D printing can create a copy of the original with the magic of a 3D printer.
Going from a virtual to a 3D-printed object one is a fairly straightforward process—made all the easier with help from the tech experts at the former UCLA’s Scholarly Innovation Laboratory (SIL). Once the digital reconstruction was complete and a virtual object was rendered [https://sketchfab.com/models/257a500a929a4bb3be56251ec3d6dc3c], we took the data from the 3D model and converted it into an .STL file. The standard file type for additive manufacturing, .STL is good for 3D print jobs of a single color. If you require multiple colors of a given material, other file formats, such as .AMF, provide that support.
File in hand, the object is prepped for 3D printing, usually meaning filling holes and gaps in the wireframe. Open-source editing programs such as Blender and MeshLab are useful, open-source tools at this stage for polishing up virtual objects. It is important to note that any texture files associated with objects rendered with photogrammetry are lost in the conversion process. Since the .AMF file will be using only the physical data points and none of the data from the photographic textures, there are bound to be some differences in the details. Our bust had a few wrinkles that were easily smoothed out.
The object file is then printed using one of the 3D printers available to the UCLA community. We wanted to make the bust as big as we could in a single print job. We also wanted to use a white filament that matched the original marble sculpture. With the assistance of Doug Daniels and his team at the UCLA Library’s Lux Lab, we were able to create a bust approximately 10 inches high—roughly 1/3 of the original size. Full-scale replicas may be constructed in multiple parts, if desired, but the smaller size was just fine for our needs.
Doug recommended using one of the Lulzbot Taz 6 printers which have the filament color we were looking for and the build volume we needed. The Taz 6 is a Fused Deposition Modeling (FDM) printer; that is, it takes a line of plastic filament, melts it down, and deposits the plastic layer by layer to build the object. Printing the bust also required a fair amount of support material to hold up the overhanging parts such as Thoreau’s distinctive nose. Once the printing is complete, the support matrix is either cut away or washed away depending on what kind of plastic is used. Finally, an acetone wash and a resin-based protective coat reduced the appearance of lines on the final product.
All told, printing at the highest resolution, the bust took over two days to print, with a material cost of less than $25. The finished product—the first and only 3D-printed Thoreau in the world—will be donated to the Walden Woods Project next year as part of the Thoreau Bicentennial celebration.
For those who are interested in 3D printing at UCLA, individuals can contact Doug at LuxLab@library.ucla.edu, or reserve time with one of the LuxLab specialists.
Featured image: The printed Thoreau bust in the UCLA Library Special Collections department.
Resources:
- Blender (https://www.blender.org/)
- Lulzbot (https://www.lulzbot.com/store/printers/lulzbot-taz-6)
- Meshlab (http://meshlab.sourceforge.net/)
- UCLA’s Lux Lab Appointment Calendar (http://calendar.library.ucla.edu/appointments/?g=685)
- UCLA’s Lux Lab Contact email (LuxLab@library.ucla.edu)
- Walden Woods Project (https://www.walden.org/)